PE/PPR pipe extrusion line
Position: Home > Product > PE/PPR pipe extrusion line >
16-63mm PPR pipe extrusion machine
Tel: +86-199-5255-2903

Suzhou Kingdom Machinery Co., Ltd.
Our main products are: plastic pipe extrusion line and plastic recycling machine.
The main products are popular in the domestic market, such as the East China market, Southwest market, Northeast market and Central China market. The products are also exported to international market, including Russia, Australia, Southeast Asia, Middle East, East Europe. Africa and other countries.
PPR Pipe.
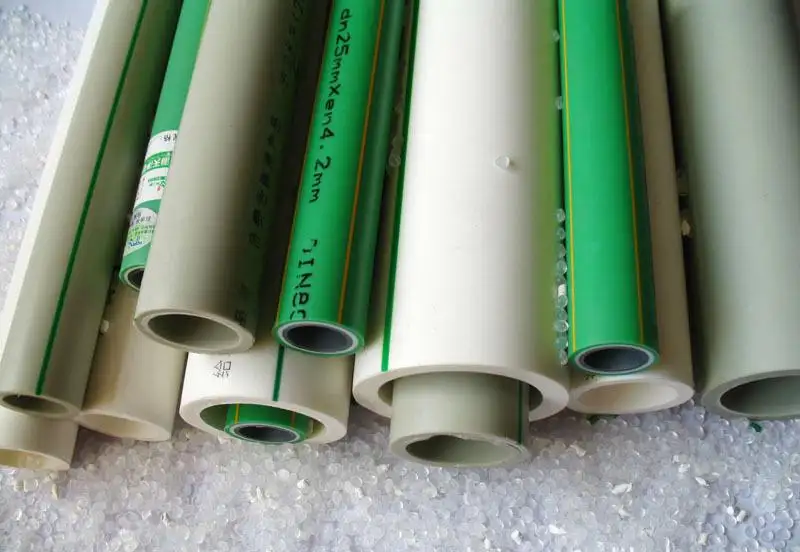
Good hygienic performance: no heavy metal salt stabilizer is added during PE pipe processing, the material is non-toxic, no scaling layer, and no bacteria breeding, which solves the hidden danger of secondary pollution of urban drinking water.
■ Excellent corrosion resistance: Except for a few strong oxidants, it can withstand the erosion of a variety of chemical media; no electrochemical corrosion.
■ Long service life: PE pipe can be used safely for more than 50 years under rated temperature and pressure .
■ Better impact resistance: PE pipe has good toughness and high impact resistance, and heavy objects directly
pass through the pipe, which will not cause the pipe to be broken.
PE/PPR Pipe Extrusion Line.
Through long time and continuous innovation and testing, Kingden has developed the new generation PE pipe extrusion line with high automation, high speed, high reliability, low energy consumption. Our PE pipe extrusion can process wide range of material, including HDPE, LDPE, PP, PPR, PPH, PPB, MPP, PERT, etc.
Our PE pipe extrusion line can produce from size of minimum 16mm to 2000mm with single layer or multi-layer.
Single Screw Extruder.
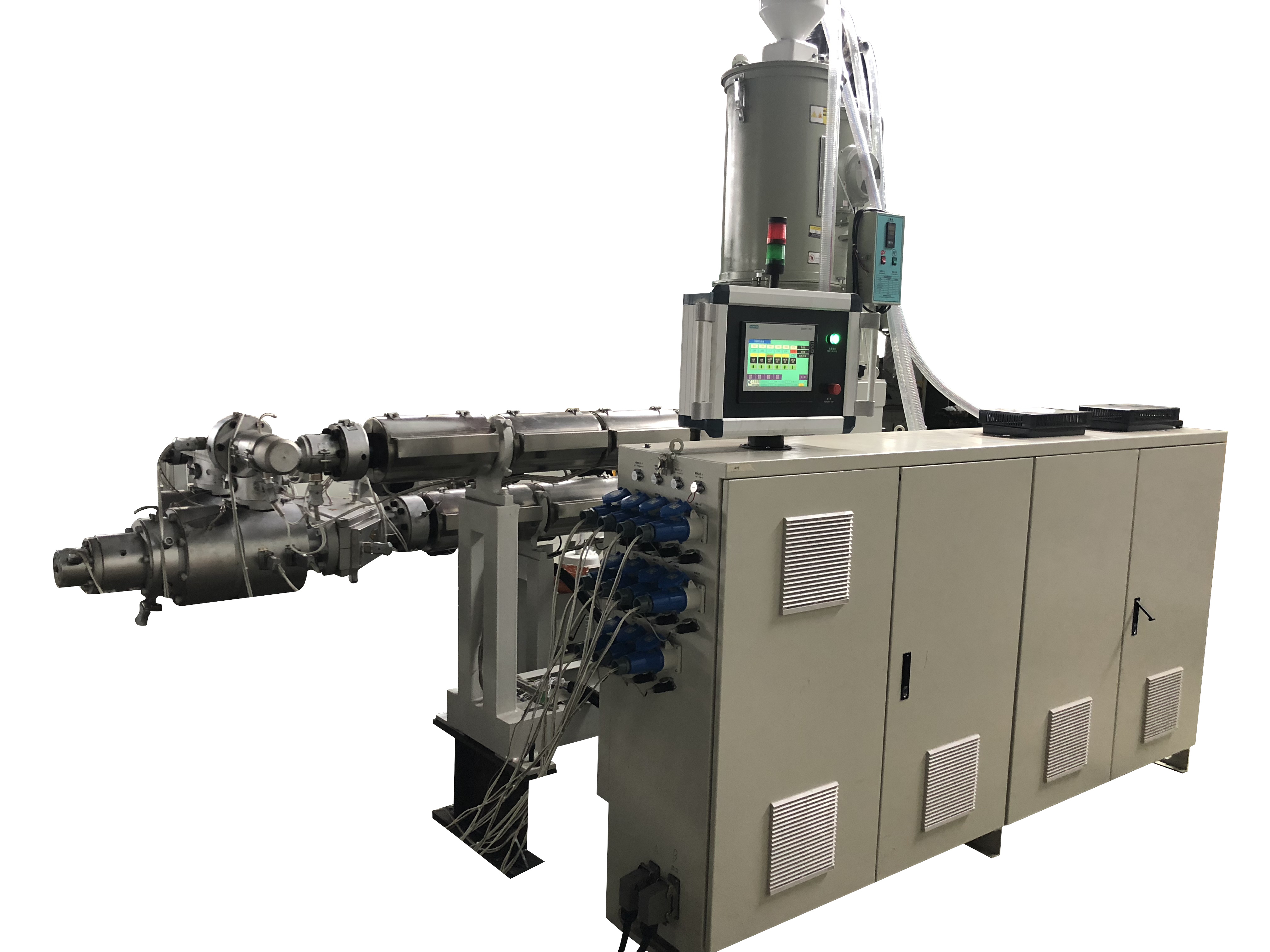
1.1 Simens Touch Screen and PLC
1.2 Spiral Structure of Barrel
1.3 Special Design of Screw
1.4 Air Cooled Ceramic Heater
1.5 High Quality Gearbox
Based on 33:1 L/D ratio for screw design, we have developed 38:1 L/D ratio. Compared with 33:1 ratio, 38:1 ratio has advantage of 100% plasticization, increase output capacity by 30%, reduce power consumption up to 30% and reach almost linear extrusion
performance.
Extrusion Die Head.
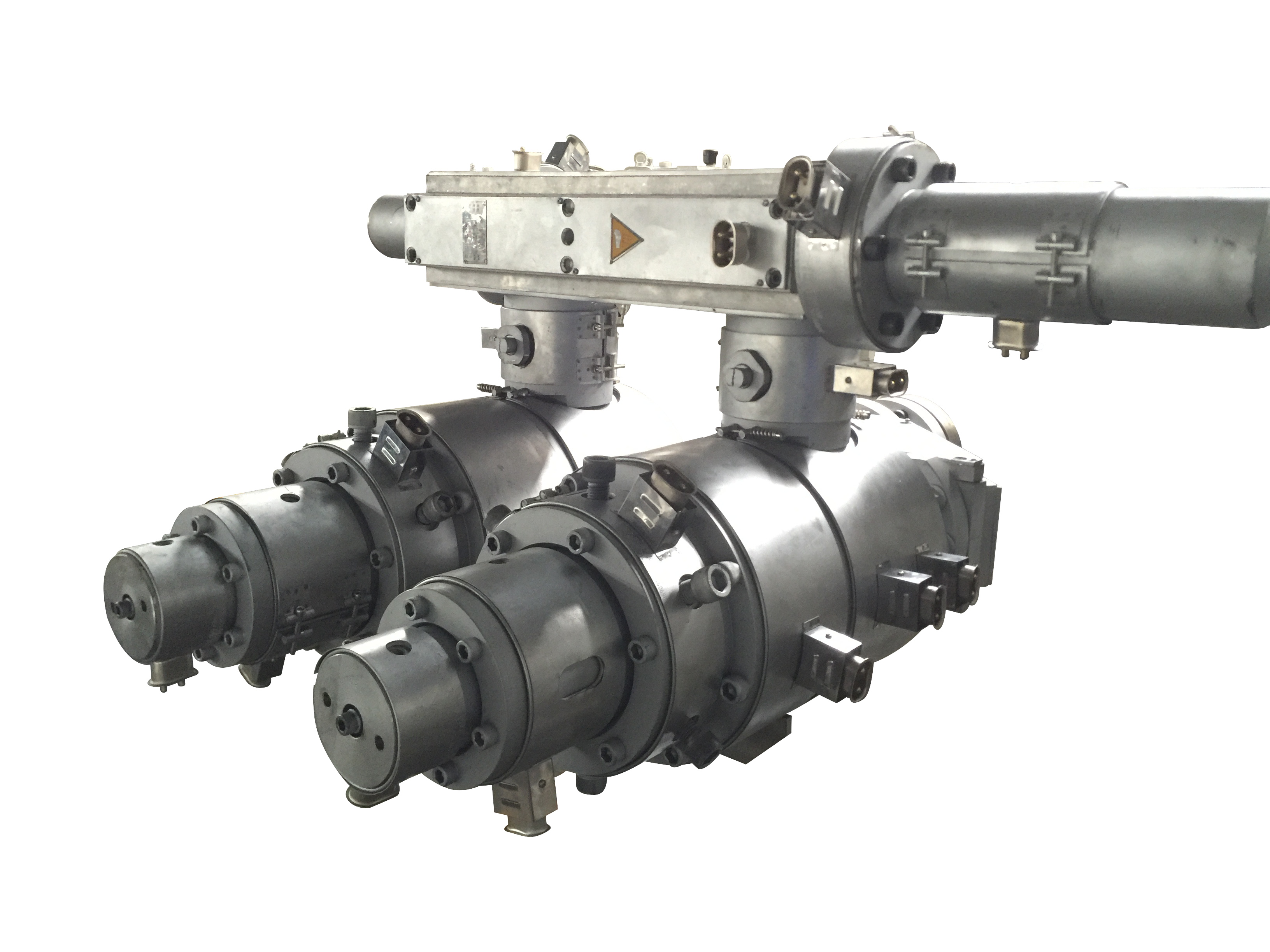
2.1 Moving Device of Die Head
2.2 Die Head Rotary Device
2.3 Heat Exhausting Device
2.4 Cooling Device for Core
Extrusion die head apply spiral structure, each material flow channel is placed evenly. Each channel is after heat treatment and mirror polishing to ensure material flow smoothly. Die head structure is compact and also provide stable pressure, always from 19 to 20Mpa. Under this pressure, pipe quality is good and very little effect on the output capacity. Can produce single layer or
multi-layer pipe.
Vacuum Tank.
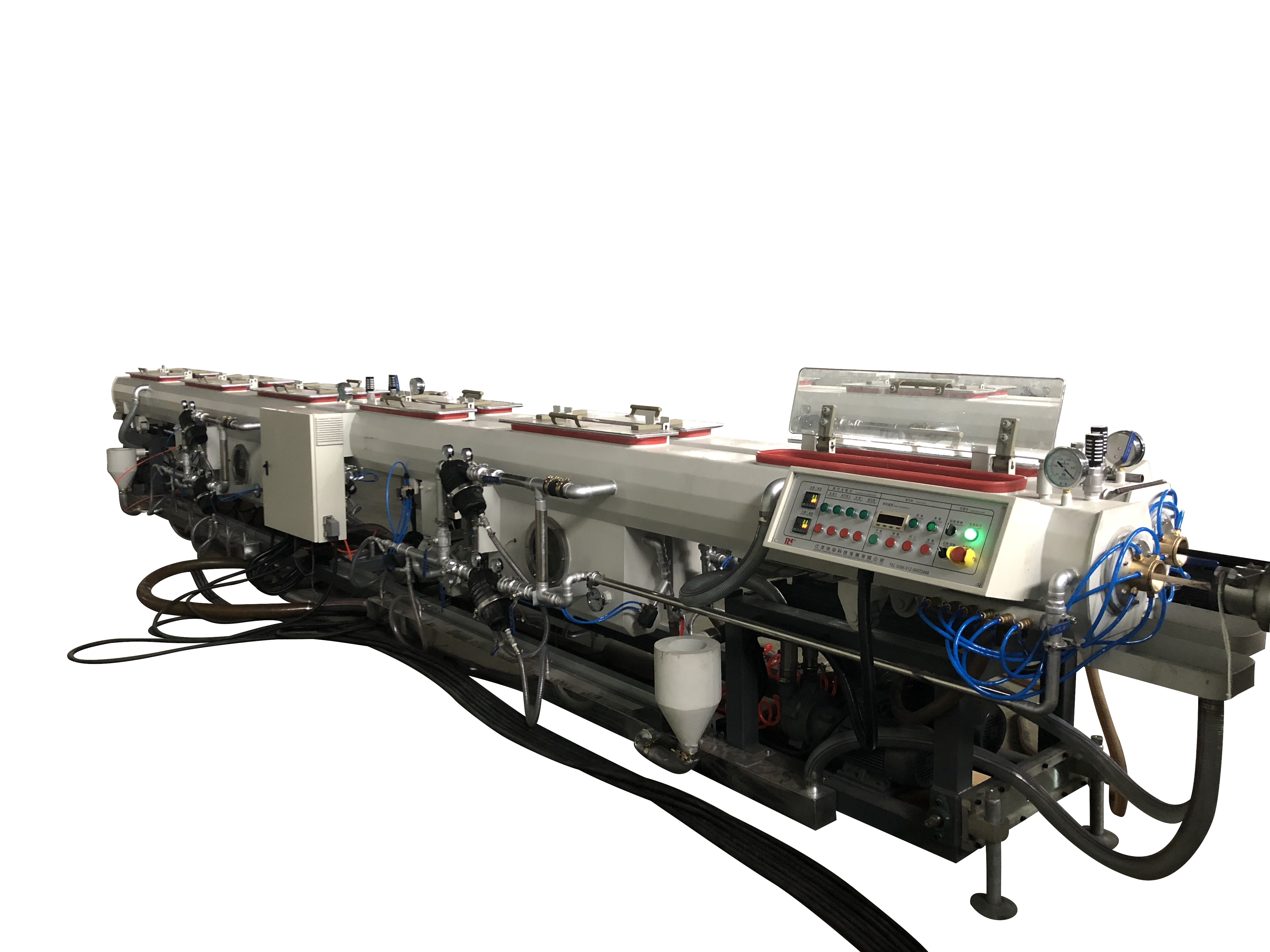
3.1 Strong Cooling for Calibrator
3.2 Better Support for Pipe
3.3 Silencer
3.4 Pressure Relief Valve
Vacuum tank is used to shape and cool pipe, so as to reach standard pipe size. We use double-chamber structure. First chamber is
in short length, to ensure very strong cooling and vacuum function. As calibrator is placed in the front of first chamber and pipe shape is formed mainly by calibrator, this design can ensure quick and better forming and cooling of pipe.
Cooling Tank.

4.1 Pipe Clamping Device
4.2 Water Tank Filter
4.3 Quality Spray Nozzle
4.4 Pipe Support Adjusting Device
4.5 Pipe Support Device
Cooling tank is used to cool pipe further.
Haul off unit.
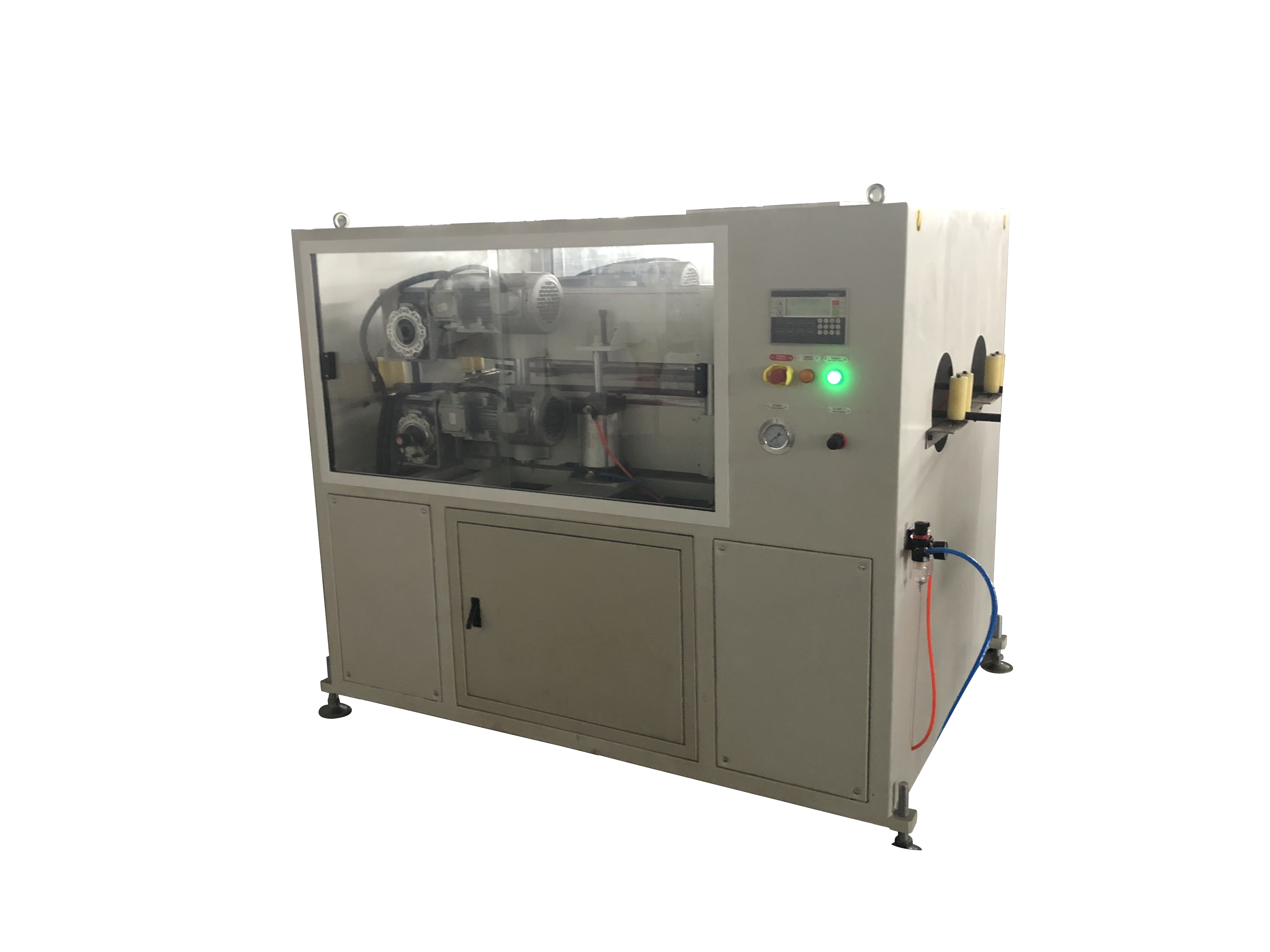
5.1 Pipe Clamping Device
5.2 Water Tank Filter
5.3 Quality Spray Nozzle
5.4 Pipe Support Adjusting Device
5.5 Pipe Support Device
Haul off unit provides sufficient traction force to pull pipe stably. According to different pipe sizes and thickness, our company will customize traction speed, number of claws, effective traction length. To ensure match pipe extrusion speed and forming speed, also avoid deformation of pipe during traction.
Cutter.
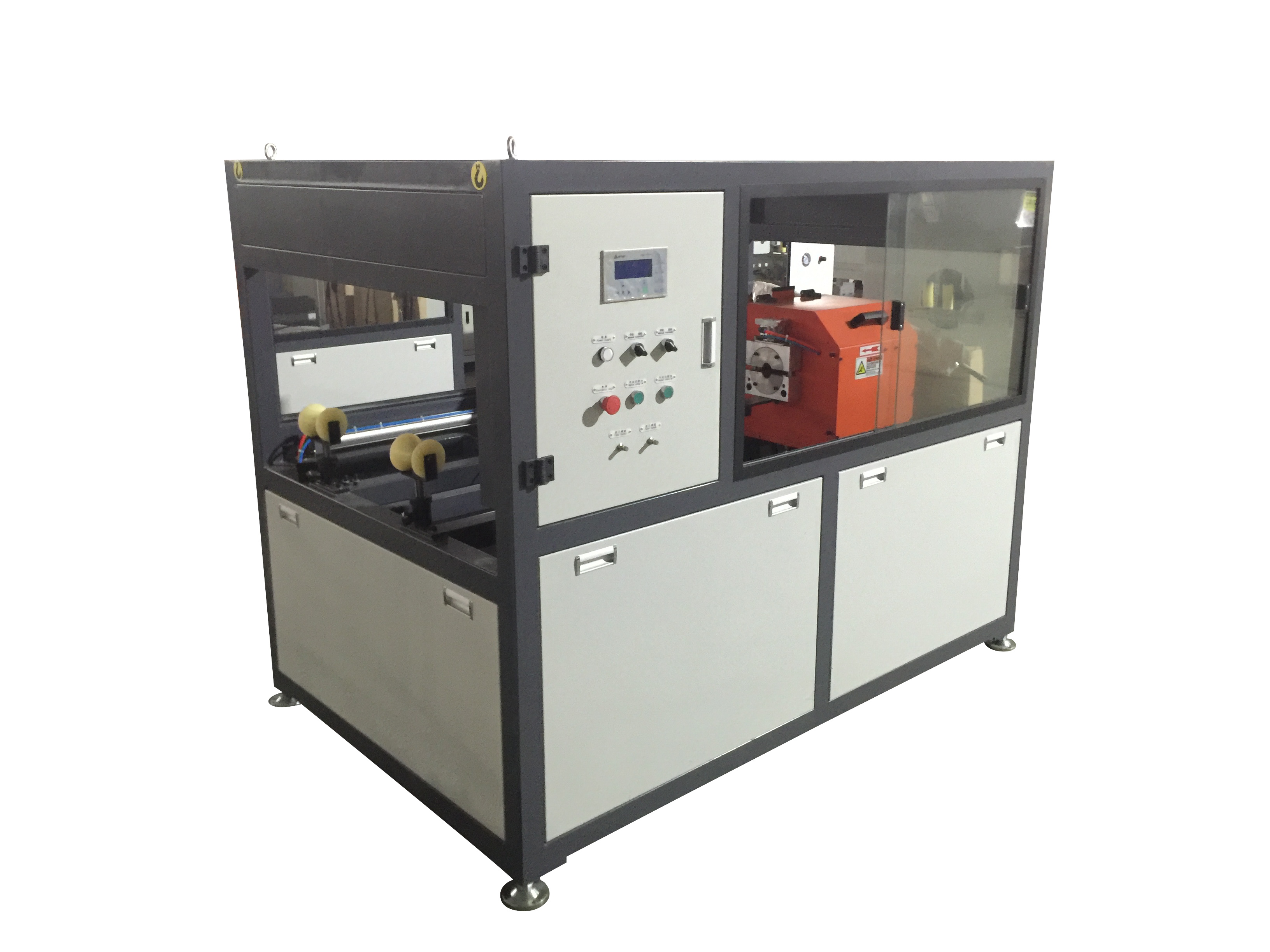
6.1 Universal Clamping Device
6.2 Central Height Adjustment
6.3 Saw and Blade Interchangeable
Cutter controlled by Siemens PLC, working together with haul off unit to have precise cutting. Customer can set the length of pipe they want to cut. Multi-feed-in actions for the accomplishment of one cutting process (protect blades and saws, prevent from blade and saws stuck for thick pipe and cut face of pipe is smooth).
Stacker.
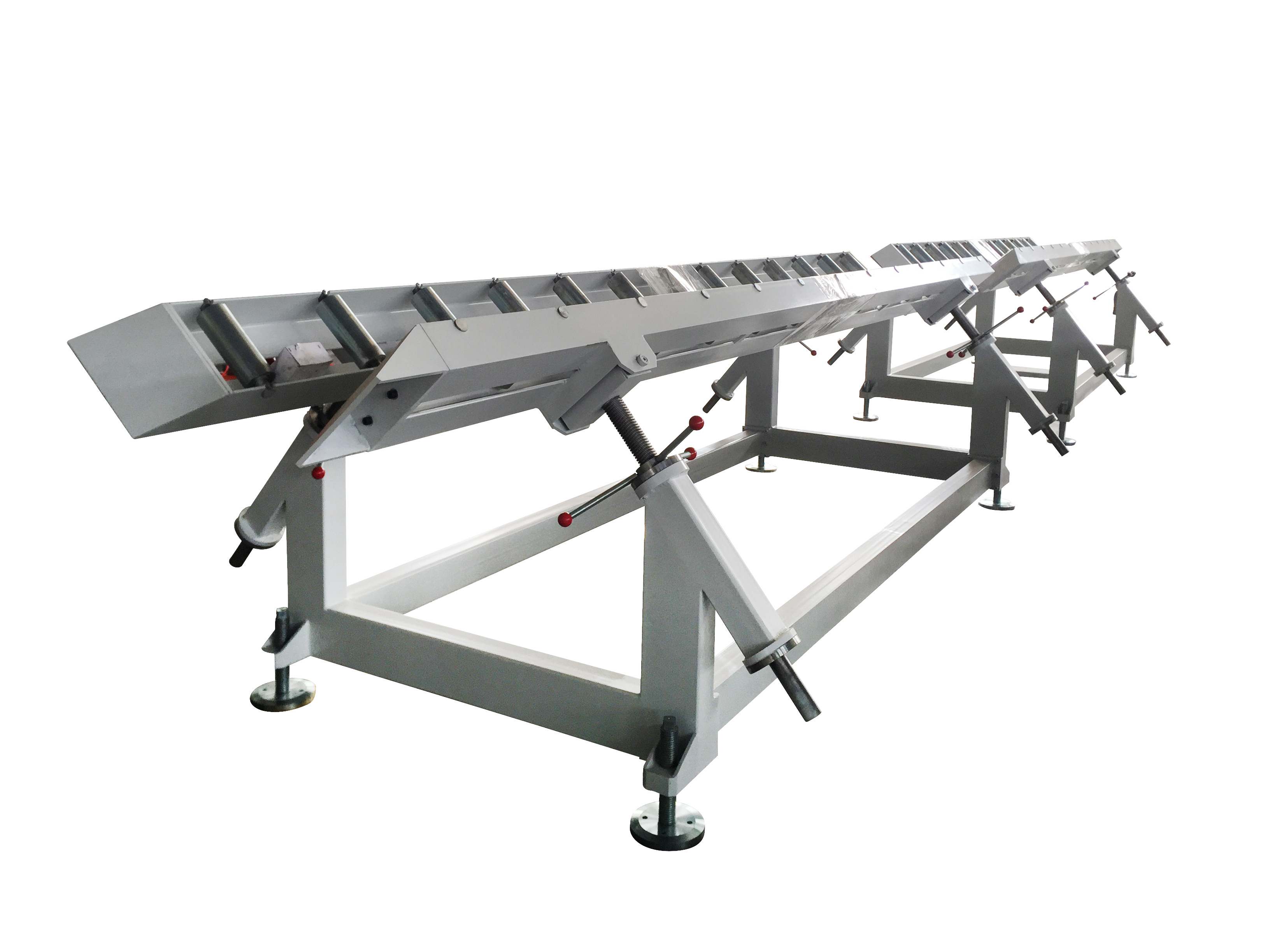
7.1 Pipe surface protection
7.2 Central Height Adjustment
To support and unload pipes. Length of stacker can be customized.
Workshop
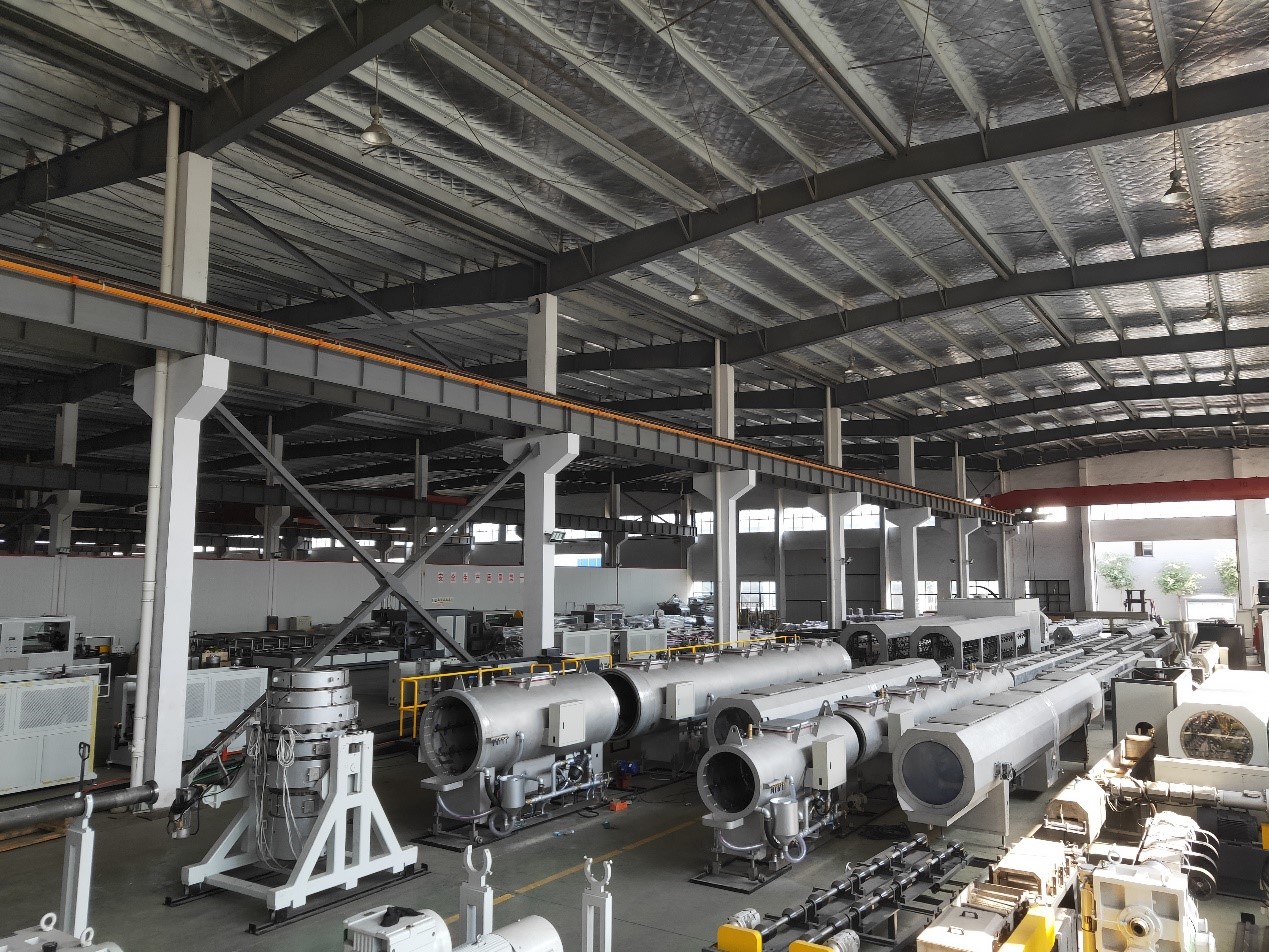
We know the quality is the life of our company. Our company insists to manufacture all machine units by ourselves in order to control quality strictly by our quality inspectors. To implement this concept, we have built our own tooling and CNC workshop. Even if some parts from our certified supplier, our quality inspector will check these parts before entering into our warehouse.
Warmly welcome to visit our workshop, and sincerely hope we can have long term cooperation in near future!
FAQ
1) Are we manufacture or trade company?
We are manufacturer, have much experiences in this field.
2) What kind machines we produce?
Our factory produce plastic pipes machines, plastic auxiliary machine.
3) What kind payment we accept?
Payment term like T/T, L/C.
4) How long we need to produce the machines?
According to different machine model and configuration , we need different time, like 40 days to 2 months.
5) Will the machine be delivered on time ?
Sure, we will deliver your machine up receiving the balance payment.
6) How about the machine quality?
Our machine quality is reliable .We select every parts on the machine strictly and production and installation is done by professional workers .We test the each production step for the best machine.
7) How about the price?
You know ,the goods counts the the price .We select the best machine raw material such as siemens electrics ,schneider and ABB etc .We will provide you the best machine with best price.
8) How long is your machine’s guarantee time?
One year
9) What can you provide for after sale service?
We can send engineers to your factory for installation and training also 24 hours on-line service for you.